Resolving Extrusion Molding Challenges with Effective Purging Compounds
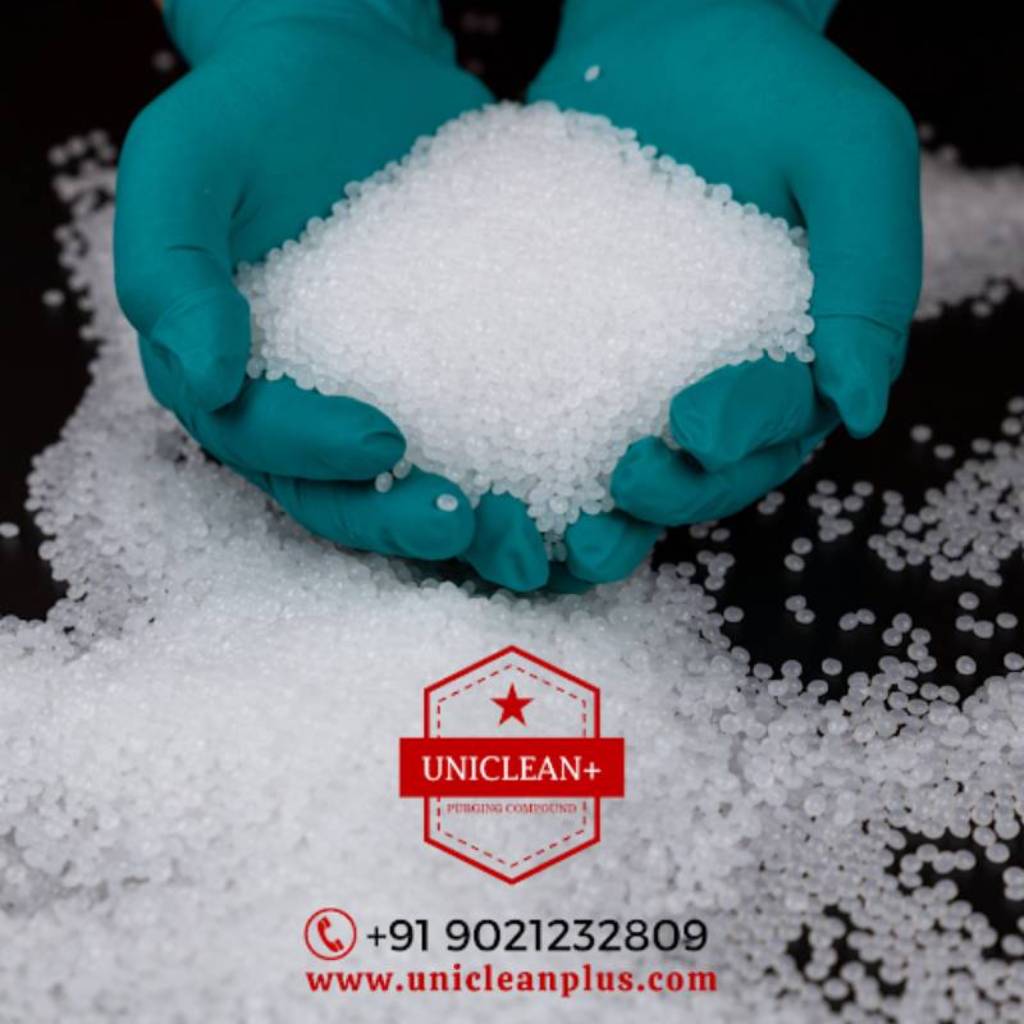
Extrusion Molding may appear seamless from the outside, but those in the industry know the myriad challenges that arise in maintaining smooth operations. From material contamination to lengthy changeover times, these issues can lead to significant production inefficiencies.
How to overcome these obstacles without halting operations or sacrificing quality? The answer lies in using the right Purging Compound for Extruders, such as the highly efficient UNICLEANPLUS™ Purging Compound.
The Challenge of Material Contamination
Material Contamination is a frequent issue during extrusion molding. Residual build-up within the barrel or screw can introduce impurities into your product, compromising quality. These contaminants may result from color changes, resin transitions, or degraded material left behind during production. Ignoring these residues can lead to wasted material and delayed timelines.
Solution: UNICLEANPLUS™ Purging Compound efficiently eliminates material build-up and contaminants. Its specialized formulation ensures thorough cleaning of the barrel, screw, and even the dies, leaving no residue behind.
Extended Changeover Times
Extrusion Molding often requires frequent material or color changes. Without proper cleaning, these transitions can lead to product inconsistencies and excessive downtime. Have you ever struggled with achieving consistent results after switching materials? This is a sign that your current cleaning process might not be effective.
Solution: With Purging Material for Extruder like UNICLEANPLUS™, you can cut down changeover times drastically. Its quick action and user-friendly process allow operators to clean the equipment efficiently, minimizing downtime and maximizing productivity.
High Scrap Rates
Scrap generation during start-up or changeover processes can be a major drain on resources. Faulty products caused by contamination or uneven material flow increase waste, which, in turn, affects your bottom line.
Solution: By Incorporating UNICLEANPLUS™ into your workflow, you reduce scrap rates significantly. Its ability to clear out residual material ensures that your extrusion runs start clean, producing high-quality products right from the beginning.
Long Downtimes Due to Maintenance
Periodic Cleaning of Extruders is essential, but traditional cleaning methods often require dismantling parts or halting operations for long periods. This can disrupt production schedules and escalate costs.
Solution: UNICLEANPLUS™ simplifies the cleaning process with a non-abrasive formulation that works directly within the system. There’s no need for extensive disassembly, making maintenance quicker and hassle-free.
Achieving Consistent Results
Uniformity is key in extrusion molding, yet inconsistencies can creep in due to equipment inefficiencies. This is especially true during prolonged runs or when switching to new materials.
Solution: UNICLEANPLUS™ ensures smooth transitions and consistent results by removing every trace of prior material, giving you a clean slate to work with every time.
UNICLEANPLUS™ delivers on all fronts—efficiency, ease of use, and cost-effectiveness. With its advanced formulation, you can overcome the challenges of extrusion molding while optimizing operations. Contact UNICLEANPLUS™ today for expert guidance and discover how our Purging Compound for Extruders can transform your production line.